INBOUND: North Ultra HM Mast
If there’s a guy who knows a thing or two about foil masts, it’s North’s Product Manager, Uli Sommerlatt. So with the introduction of their new Ultra High Modulus carbon mast, it was time to get in touch with the man who knows it inside out…
First Uli, please give us an overview of why you use ultra-high modulus carbon fiber, and what the benefits are to the rider…
Ultra-high modulus fiber allows us to design a mast with the lowest hydrodynamic drag to handle the highest loads for its size/cross-section. A standard modulus mast with the same stiffness values would need a thicker profile and, hence, increased drag. A stiffer mast gives the rider a more direct steering impulse, so when you lean into a turn or give a steering impulse, the mast will respond quicker. This allows the rider to be more radical and technical in their maneuvers, make sharper turns and accelerate faster. It also provides greater top-end speed and more low-end.
Does the HM carbon allow you more design freedom in terms of section and profile thickness?
When it comes to mast design, we always try to find the optimum balance between stiffness in bending and torsion and the reduction of hydrodynamic drag. We are trying to find the thinnest mast profile section with low drag that can still handle the required loads. So yes, HM (High Modulus) and UHM (Ultra High Modulus) carbon fiber gives us the freedom to design a thinner mast profile that can carry the same (or, in our case, even higher) loads as a thicker mast profile made from standard modulus carbon. We are actually using a combination of HM and UHM carbon in our HM mast series to get the best stiffness out of the mast.
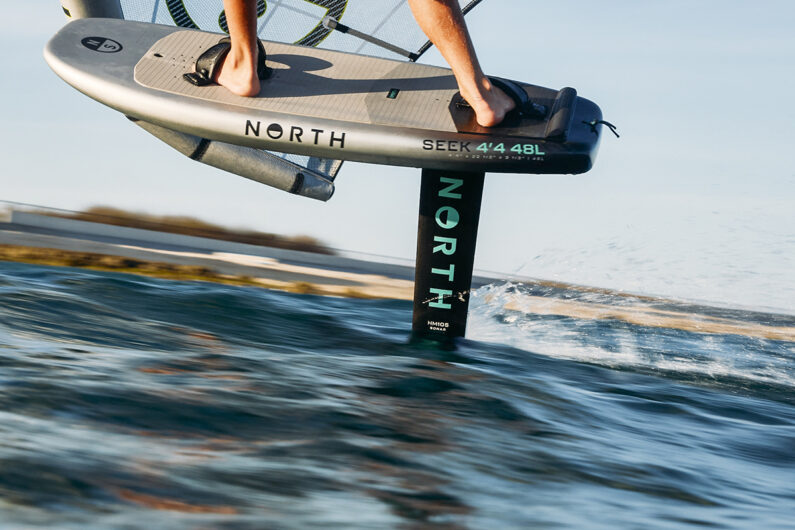
How do you find that sweet spot between stiffness and drag?
It is an iterative process. We use a combination of CFD (Computer Fluid Dynamics) and FEA (Finite Element Analysis) tools for simulation, where we study the drag curves of various mast profile sections for the speed range that we anticipate for the particular mast. We then choose a profile section with the best drag reduction and stiffness ratio over that speed range.
For a given load case scenario, we calculate the stiffness at certain heights along the mast length for the chosen profile shapes and profile thickness. This allows us to calculate the stress at any particular point along the mast length. It is basically like taking an MRI of your knee, where you run through a complex 3D structure broken down into thin 2D sections along the length of your leg to analyze it. Generally, the thinner the profile, the less drag it will create. However, there are foil sections that will create less drag than the other, even if the thickness would be the same for both. So, profile thickness alone is not a measure for low drag. It gives a good indication, but choosing the right foil section where the sweet spot sits between low drag and maximum stiffness makes a good mast design at a competitive weight.
We understand you haven’t just built a template for these masts and run with it… instead, they vary between sizes right?
If you want ultimate performance, you can't take the one-profile-section-fits-it-all approach and just chop the mast into different lengths. We designed each mast length separately from the others to fit the various characteristics required for the different foiling conditions and disciplines. From an engineering side, working with carbon composites allows us total freedom of shape (within reason). So why not take advantage of this freedom and cater to what is needed for each mast size and how the rider will use it?
Are the masts completely backward compatible with the existing system?
Everything in the North Sonar Foil System is interchangeable and backwards compatible. We weren't the first brand to bring a foil system to market when we started the Sonar foil range five years ago. That gave us the opportunity and advantage to really look at what matters in a sound foil system and the key areas that need special attention. These have always been the connection points between components – board to mast, mast to fuselage, fuselage to front wing and stabilizer. If these are well-designed, you'll retain a lot of energy from steering impulses or pumping, especially with bigger front wings. If they are wobbly, you will feel a delay in the response of your steering commands, and the foil system will feel sluggish and unresponsive. Basically, you are losing the necessary energy and efficiency for nothing. You and your gear can't operate at its optimum. So, we designed a low-maintenance connection system that allowed the best load transfer and usability. We call the mast to fuselage connection ‘GeoLock'. Here the mast sits inside a tapered recess within the fuselage and gets held down by two M8 screws. Most of the load gets transferred over the tapered geometry fit between the two parts, ensuring a rock-solid and long-lasting connection. We designed a modular foil system that feels and performs as close as possible to a one-piece foil setup where the mast, fuselage, front wings, and stabilizer are permanently bonded or connected.
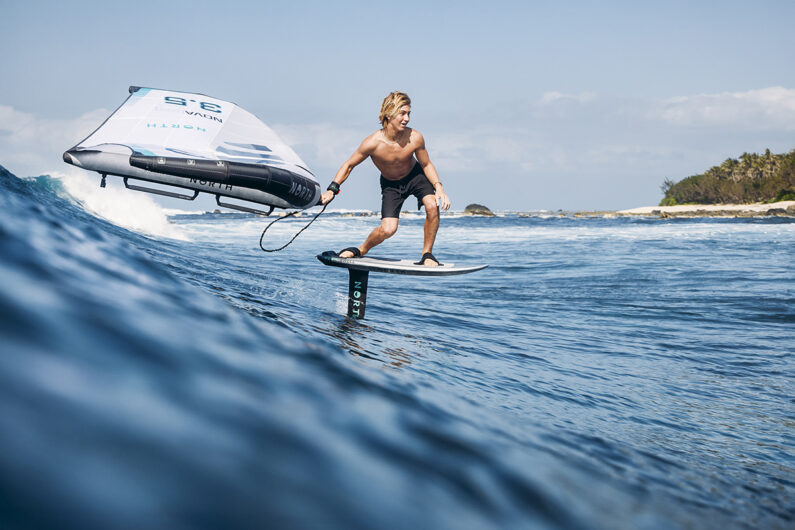
What system do you use to bench test the mast stiffness?
We have a test jig where we bolt the mast to the wall and test three load cases, which allows us to give a very accurate measure of the stiffness of any mast independent of their length. Therefore, we define here three different load cases:
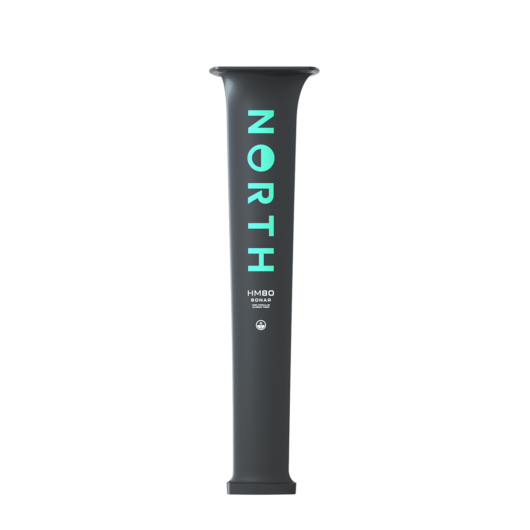 |
Cantilever bending stiffness
This load case is equivalent to when you ride upwind. While heeling over, you create a bending moment in the mast with your body weight. As you tack or roll the board into a turn, you will feel how quickly the foil reacts to the load change from your body weight (rail to rail) – a measure of the mast's bending stiffness. Here, we hang a weight on the mast end and measure the mast's deflection under the load of the weight.
|
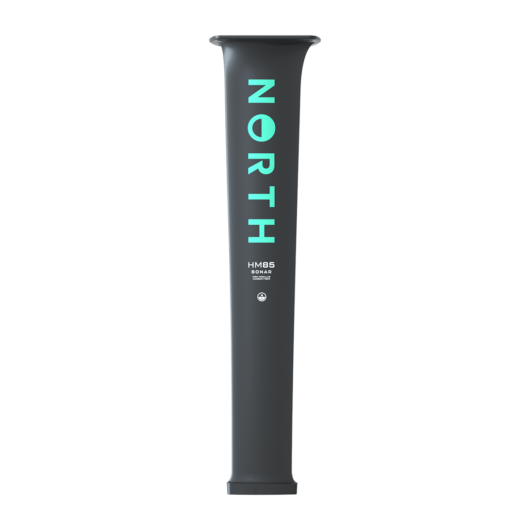 |
Eccentric bending stiffness
This load case is equivalent to landing after a jump with the foil. Here, most of the time, one side of the front wing touches the water first, creating an off-centric bedding moment in the mast combined with a torsional moment. Here, we attach a line at a given height along the span of the mast and pull the line towards the wall with a deflection block on which a weight is attached. We measure the deflection of the mast and the angle change/twist of the mast under load.
|
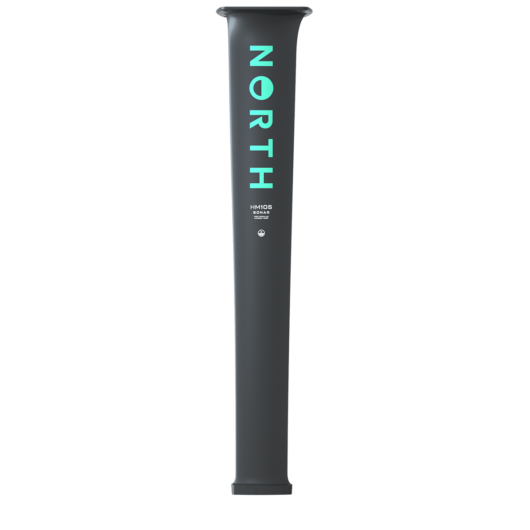 |
Torsional bending stiffness
If you turn your board upside down with the foil attached, put your foot on the board so it can't move, grab the tip of the front wing and the opposing tip of the stabilizer and try to rotate them clockwise or anticlockwise; you will feel the torsional stiffness of your mast. Torsional stiffness is what you feel when you give any steering impulse with your feet or body weight to the foil to change direction or navigate through a turn. The stiffer the mast is torsionally, the more direct the foil system's response will feel. Here, we hang a weight at a given distance from the mast at the end of the fuselage and measure the angle change/ twist of the mast.
|
After all this, we ride the foils to verify if the results we see in our measured values match reality. This has been spot-on so far.
Is there any way to measure how much the mast reflexes and stores energy?
The material properties mainly drive this –SM and HM carbon have different spring-back characteristics. The more a mast deflects, the more energy it can store, but if it deflects too much, a foil system can feel sluggish or wobbly.
What sort of rider should opt for the HM Mast?
Anyone keen to improve the efficiency and performance of their foil system. The heavier the rider, the harder it becomes to find an efficient foil system, so riders above 90kg will benefit the most from the increased stiffness. Lighter riders will enjoy the crisper response, reduced drag, and better glide and pumpability.
How’s the feedback been from the team riders who’ve been using these masts?
The feedback has been overwhelming regardless of rider experience or discipline. Every rider reported a massive boost in their foiling skills. We don't just test with our team riders but also extensively with novice to intermediate-level riders. The products we design need to work for the newcomers to the sport as well as they do for the seasoned rider. That said, intermediate to advanced-level riders will benefit the most from the HM Mast Series' performance gains. The response, the acceleration and the glide – everything feels more efficient and effortless.